In 2024, the global 3D printing market was valued at $16.75 billion, with a projected compound annual growth rate (CAGR) of 23.3% through 2030 according to Grand View Research. This growth is fueled by advancements in materials, technologies, and applications, making 3D printing an essential tool for designers, brands, and enthusiasts.
3D Printing Fashion Breakthroughs in 2024 and Early 2025
3D printing enables designers to create bespoke items tailored to individual preferences and body shapes. Here are a few tricks that we have seen brands doing:
Customization and Personalization with 3D Printing and AI
Nike’s A.I.R series, for example, uses AI-generated, 3D-printed designs to offer personalized sneakers for athletes like Sha’Carri Richardson and Victor Wembanyama. Through this new program that Nike has established with Zellerfeld, chief executive officer Cornelius Schmitt emphasized that designers and brands are now able to rapidly bring new concepts to market, while consumers can access a diverse, ever-expanding range of footwear. The CEO noted that for the platform aims to “demolish traditional financial and logistical barriers” when creating footwear, allowing real-time experimentation and product refinement.
Syntilay on the other hand, has also introduced the world’s first AI-designed, 3D-printed shoes tailored to individual foot specifications. Utilizing artificial intelligence, 70% of the shoe’s design was generated, resulting in a custom-fit product that combines futuristic aesthetics with personalized comfort.
Advancements in Custom Apparel Manufacturing
The rise of Direct-to-Shape inkjet printers has enabled the printing of detailed and colorful designs directly onto garments. This advancement offers designers greater freedom and flexibility in creating custom apparel, enhancing the personalization of fashion items.
Promoting Inclusivity and Personalization
3D printing technology has facilitated the creation of custom-made collections tailored to diverse body types and personal preferences. This approach addresses the limitations of mass production, offering more inclusive and personalized fashion options.
Material Innovation, Sustainability and Waste Reduction
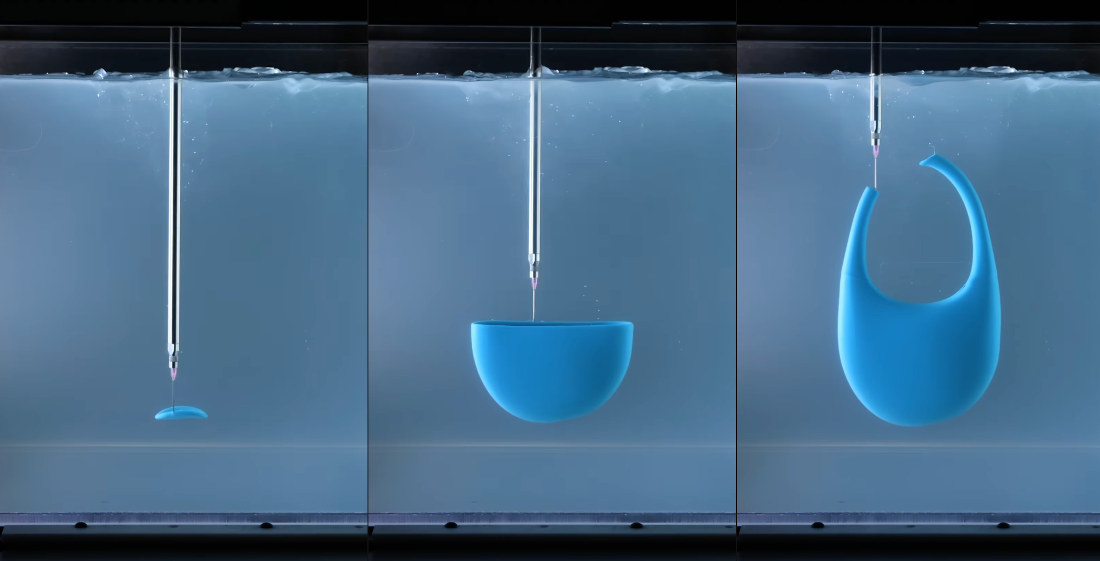
The range of materials used in 3D printing has expanded significantly, from traditional plastics like PLA and ABS to advanced options such as new favorites: biodegradable polymers, resins, and metal alloys. Designers like Coperni unveiled a gravity-defying gel bag crafted using Rapid Liquid Print (RLP) technology. RLP allows for the creation of soft, stretchable, and durable products, exemplifying the fusion of fashion and advanced manufacturing techniques. Meanwhile, Neri Oxman’s O° platform uses polyhydroxyalkanoates (PHAs) to create fully biodegradable wearables.
On sustainability, Adidas’ Futurecraft 4D Climamog sneakers feature 3D-printed midsoles made from recycled materials, showcasing how the technology can align with eco-conscious practices. McCartney’s 2024 collection featured biodegradable filaments, while Balenciaga’s Fall/Winter line included 3D-printed resin elements polished in chrome, blending luxury with eco-consciousness. Traditional manufacturing methods often result in up to 30% fabric waste, whereas 3D printing uses only the exact amount of material required for a design.
The Surge of DIY Designers Using 3D Printing at Home
The cost of 3D printers has dropped significantly, making them accessible to a wider audience. Entry-level 3D printers, such as the Bambu Lab A1 mini, are now available for under $350, offering plug-and-play functionality for beginners. For hobbyists, mid-range models like the Bambu Lab P1S (priced under $1,000) provide advanced features such as multi-material printing and high-speed capabilities, catering to more experienced users.
This price reduction has enabled DIY designers to experiment with 3D printing at home, creating custom products, prototypes, and even functional parts for personal projects. Platforms like Thingiverse and Cults3D have seen a 40% increase in downloadable designs, further lowering the barrier to entry for consumers.
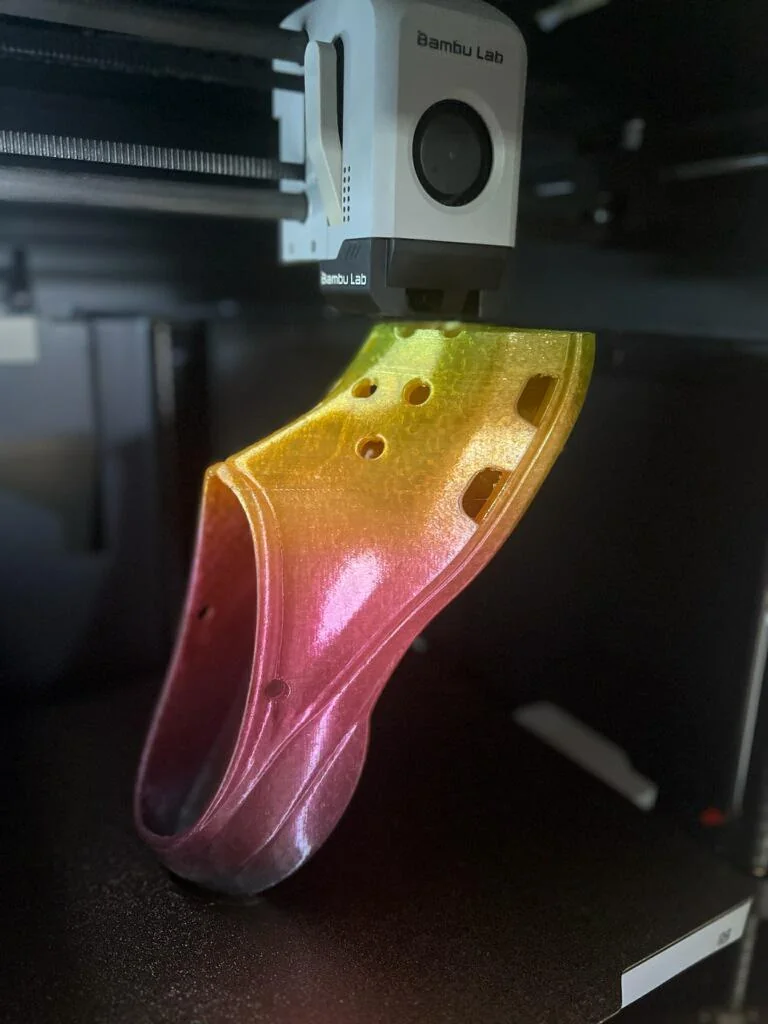
This trend is driven by the accessibility of user-friendly software like Clo3D, Blender, and Nomad Sculpt, enabling designers across various fields—from graphic designers to professional 3D artists—to seamlessly translate digital models into physical products, regardless of their 3D modeling expertise.
The Rise of Public Resources: Makerspaces, Public Workshops, Online Courses
Makerspaces like NYC Resistor in New York, London Hackspace, TechShop in San Francisco, and the Paris FabLab network are leading the charge in making 3D printing accessible, while there are an increasing number of local libraries and colleges that also offer free resources for you to explore.
For those unable to access physical makerspaces, online courses have become a popular alternative. Platforms like Youtube, Coursera, Udemy, and Skillshare offer comprehensive courses on 3D printing, covering topics such as design, modeling, and post-processing. Institutions like Footwearology Lab, LCI Barcelona and MIT have also introduced online modules, making high-quality education accessible to a global audience.
Challenges Continue in 3D Printing: Costs, Recycling, and Infrastructure
Despite new breakthroughs in 2024, 3D printing in fashion faced hurdles in 2024. High costs remained a barrier, with advanced printers and materials often priced out of reach for smaller designers. Neri Oxman acknowledged this, stating, “Scaling sustainable technologies like the O° platform requires significant investment in infrastructure and education.”
Reddit users engaged in discussions about fashion and 3D printing often highlight several challenges associated with integrating these technologies. A prominent concern is the limitation of materials suitable for wearable garments. Many 3D printing materials, primarily plastics, lack the flexibility and comfort required for clothing, making them more appropriate for accessories or structural components rather than everyday wear.
Another significant challenge is the technical complexity involved in designing and producing 3D-printed wearable items. Users note that creating intricate designs necessitates proficiency in CAD software and a deep understanding of 3D printing processes to perfect a print. Additionally, achieving high-quality prints often requires advanced, and sometimes costly, equipment. The prototyping process can be a barrier for individuals or small designers looking to experiment with 3D-printed fashion. If you didn’t know, there is literally a Reddit group named r/FixMyPrint.

Durability and practicality of 3D-printed garments are also points of discussion. Some users share experiences of creating 3D-printed clothing items, such as flexible meshes, but acknowledge that these pieces may not withstand regular use or washing, limiting their practicality. This raises questions about the feasibility of 3D-printed fashion for everyday wear and the need for further material innovation. (Reddit: 3D Printed my NYE Dress)
Despite these challenges, the Reddit community remains enthusiastic about the potential. There is a shared interest in exploring new materials, improving printing techniques, and developing designs that combine aesthetics with functionality. Collaborative efforts within these online communities aim to overcome current limitations and advance the integration of 3D printing into the fashion industry.