Neri Oxman’s OXMAN LAB has launched the first 100% biodegradable PHA shoes and apparel collection. The collection utilizes their own O° design platform, a never-seen-before innovative system that integrates digital, material, biological, and robotic technologies. This platform enables the production of the collection’s fully biodegradable consumer products using a single organic material. By eliminating the need for petrochemicals, it significantly reduces environmental impact and truly takes 3D printing to another level. It disrupts every step of sustainable consumer product 3D printing production.
The Design Ethos behind the O° 100% Biodegradable 3D Printed Shoes
“Can products grow and decompose as ecosystems? Can we design the life cycles of consumer goods to borrow matter and energy from Nature and return them upon obsolescence?” These questions drive OXMAN’s O° project to remove the complexity involved in the fabrication of objects by tuning a single and versatile mono-material class known for its biodegradability in ambient conditions and its ability to be produced from feedstocks such as atmospheric carbon dioxide or methane.
Traditional shoes often contribute to landfill waste due to their plastic components. OXMAN addresses this sustinability issue with the O° shoes and apparel collection, utilizing advanced polyhydroxyalkanoates (PHA)—a biodegradable and bio-based polymer used in 3D printing as an alternative to traditional plastics like PLA and ABS. It is produced by bacteria through the fermentation of organic materials and is known for its biodegradability, flexibility, and toughness. The production process eliminates the need for glues and petrochemicals and avoids the creation of microplastics.
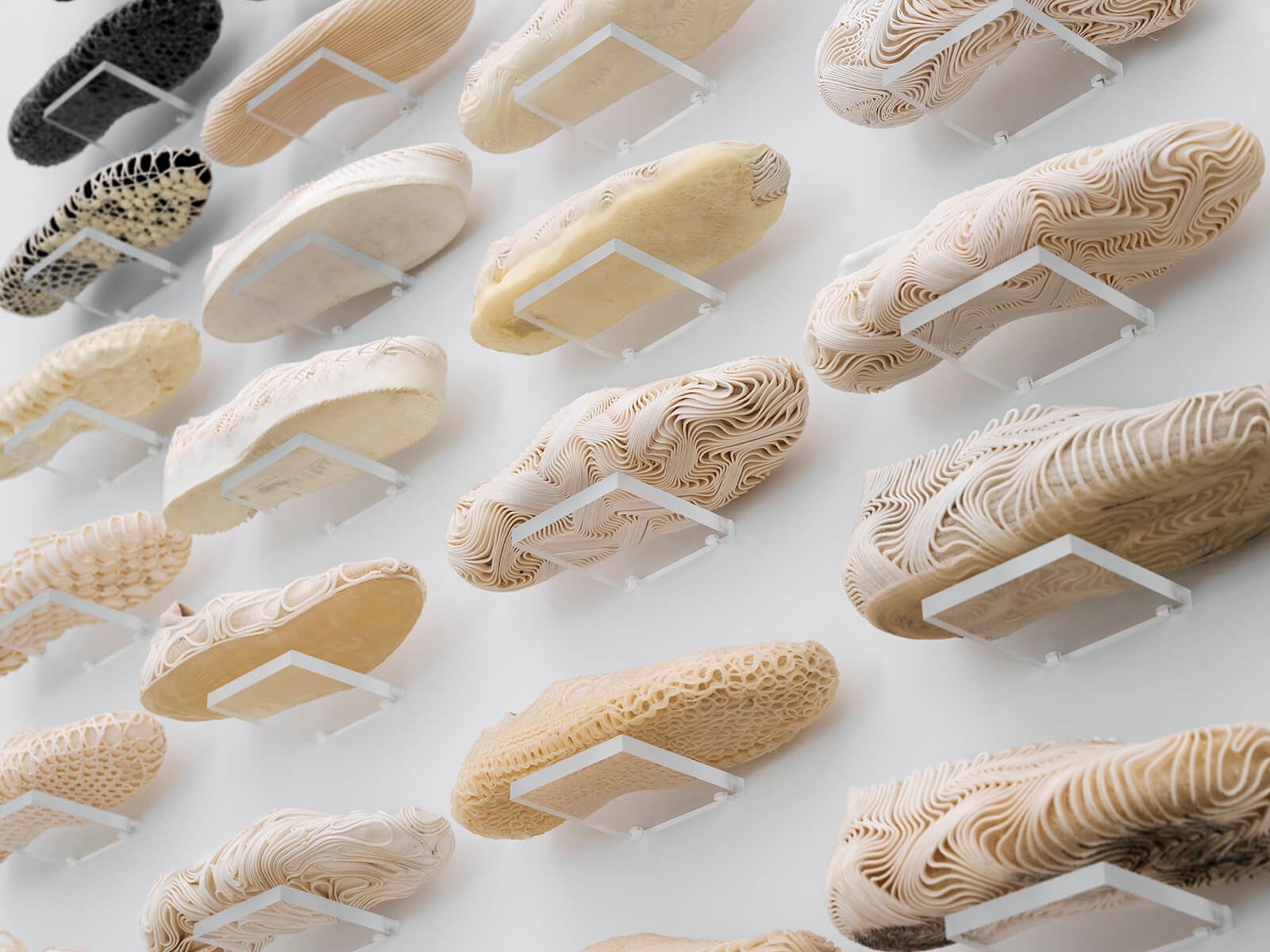
The O° shoes drew inspiration from the kinetics of human motion, requiring strict standards for comfort, robustness, and aesthetics. At OXMAN’s biofactory, each shoe emerges from a seamless fusion of knit and print—but not in the way you’re thinking. Their process starts with a base layer that’s knitted from living materials, then gets real interesting: they’re literally growing reinforcement, cushioning, and support structures directly onto the fabric. Whether its for marathon runners or studio dancers, this biological architecture adapts without switching materials or adding waste. The 3D-printed elements bond with the knit at a molecular level, creating targeted zones of strength and flex that traditional manufacturing cannot accomplish. We will look into the details of creating this design below.
The Design Platform Behind the Process: O°
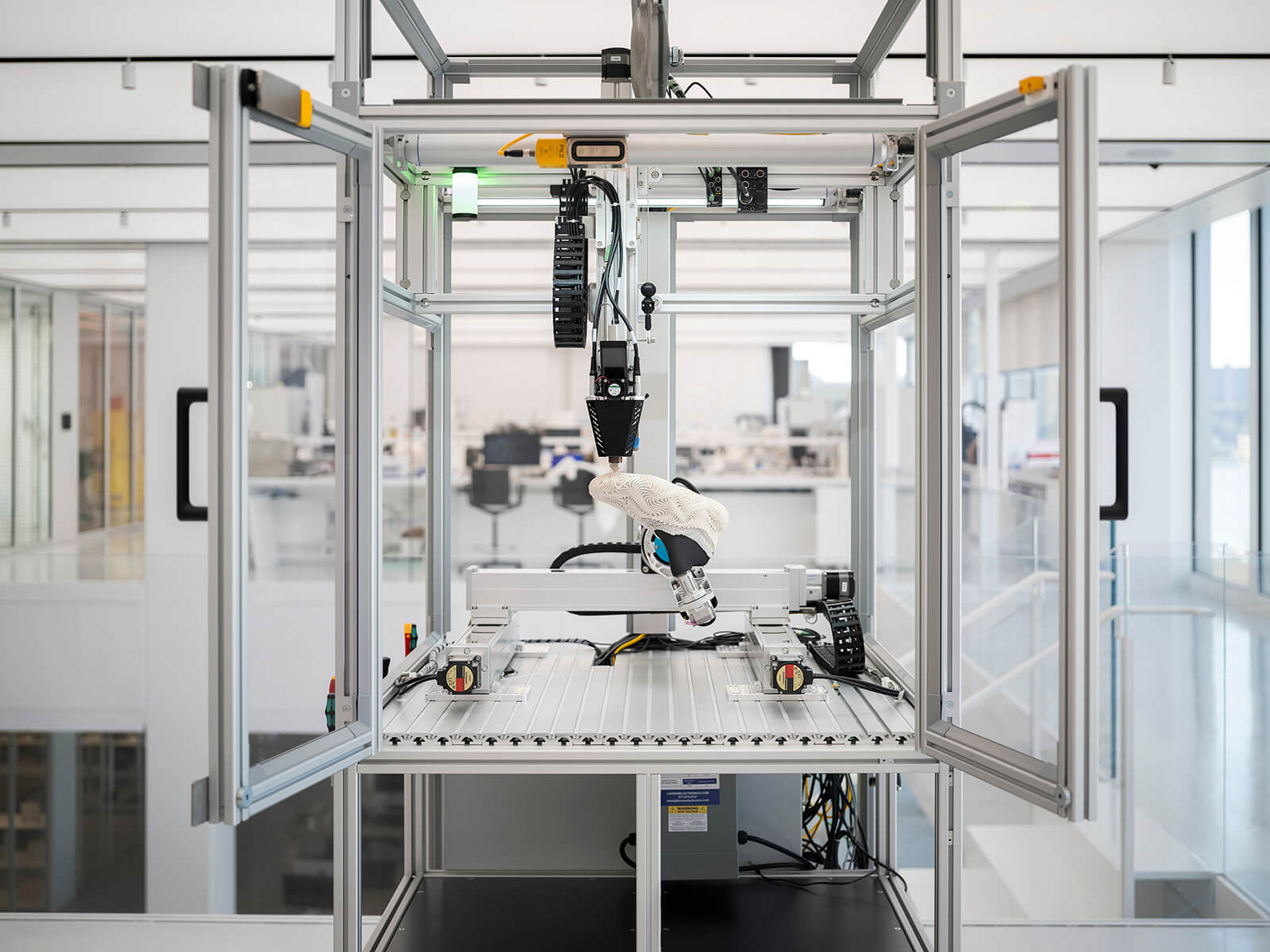
The O° platform is composed of tools, techniques, and technologies in the areas of biopolymer engineering, fiber production, and processing, as well as performance-driven computational design, knitting, and robotic fabrication. It revolutionizes traditional manufacturing processes by utilizing a single organic material, enabling the creation of consumer products under one roof with minimal human intervention.
By using this knitting and printing technology to create shape and movement, OXMAN has eliminated the cut-and-sew and adhesion processes associated with traditional shoe assembly. The O° technology offers a near-zero-waste production process and requires minimal human involvement and intervention, enabling local, low-cost production and minimizing the transport cost and environmental impact of the distant supply chains typical of the shoe industry.
Inside the O° Collection: A Disruptive Design & Production Workflow
The O° collection by OXMAN integrates multiple disciplines—chemistry, textiles, robotics, pigmentation, computation, and branding—to create biodegradable and adaptive products. Here’s how each plays a role:
1. Chemistry & Biopolymer Science
- The project relies on polyhydroxyalkanoates (PHAs), a class of bioplastics naturally produced by bacteria.
- Engineered E. coli bacteria synthesize PHAs, which serve as the foundational material for fabrication.
- Unlike conventional synthetic polymers, PHAs are fully biodegradable and break down naturally in soil and water.
- Green chemistry principles ensure that these materials leave no harmful residue, unlike petrochemical-based plastics.
2. Textiles & Material Engineering

- The O° project integrates knitting, spinning, and 3D printing to manipulate PHAs into textiles with varying mechanical properties.
- By using these techniques, the fabric can be customized for different applications, from lightweight, breathable textiles to rigid, structured designs.
- Hot melt spinning and knitting create soft, flexible layers, while 3D printing adds reinforcement where necessary.
3. Robotics & Digital Fabrication

- The project employs robotic manufacturing to assemble products in a vertically integrated system.
- This system combines digital fabrication (knitting, spinning, and printing) in a seamless workflow.
- Unlike traditional footwear and textile manufacturing, which requires various materials and complex assembly processes, robotic fabrication enables precision manufacturing with a single biodegradable material and minimal human assistance.
4. Pigmentation & Biological Coloration
- Instead of using synthetic dyes (which contribute to pollution), the project explores bio-pigmentation.
- This could involve genetically engineered bacteria or fungi that naturally produce pigments, offering an eco-friendly alternative to chemical dyes.
- Pigmentation could be embedded at the molecular level within the PHA biopolymer, ensuring the color remains integral to the material without external coatings.
5. Computation & AI-Driven Design
- Computational design algorithms dictate how materials are distributed across the product, ensuring the perfect balance of flexibility, strength, and biodegradability.
- These algorithms analyze biomechanics, stress points, and wear patterns, optimizing the material layout for different activities (e.g., marathon running vs. studio dancing).
- AI-driven simulations ensure the structural integrity of the shoes without relying on traditional prototyping, reducing material waste.
6. Integration of Nature & Technology

- OXMAN’s philosophy integrates natural growth and decay cycles into the design process.
- The project draws inspiration from natural material systems like chitin in insect exoskeletons and cellulose in plant fibers—both of which exhibit high performance through minor molecular modifications.
- By designing products that decompose as naturally as they grow, O° envisions a future where consumer goods leave no trace after their lifecycle ends.
The Future of Biofabrication
The O° project is a step towards programmable biodegradability, where materials are not just recyclable but actively return to nature. For the tech and design community that’s been waiting for innovative solutions to our plastic problem, this is an inspirational proof of concept that could revolutionize how we think about R&D. It highlights a future where:
- Materials are grown, not manufactured.
- Textiles are biologically programmed to adapt.
- AI, robotics, and biology work together to create sustainable products.
All images and project details are from OXMAN.